News detail
Application and usage method of stainless steel elbow
Author:FIRDAOS Time:2023-12-24 14:16:43 click168
Application and usage method of stainless steel elbow
Stainless steel welded elbows do not cause corrosion, pitting, rusting, or wear. In pipeline systems, stainless steel elbows are fittings that change the direction of the pipeline. According to angles, there are three commonly used types: 45 °, 90 °, and 180 °. In addition, according to engineering needs, there are other abnormal angle elbows such as 60 °. The materials of elbows include cast iron, stainless steel, alloy steel, malleable cast iron, carbon steel, non-ferrous metals, and plastics. The methods of connecting pipes include direct welding (commonly used), flange connection, threaded connection, and socket connection. According to production processes, they can be divided into: welded elbow, stamped elbow Casting elbows, etc. are commonly used fittings in pipeline installation for connecting pipes at bends. Other names include 90 degree elbows, right angle bends, love bends, etc
Equal Elbow
Usage: Connect two pipes with the same nominal diameter to make a 90 degree turn in the pipeline
1. Divide carbon steel, cast steel, alloy steel, stainless steel, copper, aluminum alloy, plastic, argon carbide, ppc, etc. by material
2. According to the production method, it can be divided into pushing, pressing, forging, casting, etc
3. According to manufacturing standards, stainless steel can be divided into national standards, electrical standards, water standards, American standards, German standards, Japanese standards, Russian standards, etc. Stainless steel is also one of the materials with strength in building metal materials. Due to its good reporting ability, stainless steel can maintain the integrity of structural components in engineering design. Chromium containing stainless steel also combines mechanical strength and high ductility, making it easy to process and manufacture components, It can meet the needs of architects and structural designers. All metals react with oxygen in the atmosphere to form an oxide film on the surface. Unfortunately, the iron oxide formed on ordinary carbon steel continues to oxidize, causing corrosion to expand and eventually forming pores. Paint or oxidation resistant metals (such as zinc, nickel, and chromium) can be used for electroplating to protect the surface of carbon steel, but as people know, This type of protection is only a thin film. If the protective layer is damaged, the steel below begins to rust
Steel that is resistant to weak corrosive media such as air, steam, water, and chemical corrosive media such as acid, alkali, and salt, also known as stainless steel and acid resistant steel. In practical applications, steel that is resistant to weak corrosive media is often referred to as stainless steel, while steel that is resistant to chemical media is referred to as acid resistant steel. Due to the differences in chemical composition between the two, the former is not resistant to chemical media corrosion, The latter generally has rust resistance. The corrosion resistance of stainless steel depends on the alloying elements contained in the steel. Chromium is the basic element that gives stainless steel corrosion resistance. When the chromium content in the steel reaches about 1.2%, chromium reacts with oxygen in the corrosive medium to form a thin oxide film (self passivation film) on the surface of the steel, which can prevent further corrosion of the steel substrate. In addition to chromium, commonly used alloying elements include nickel, molybdenum, titanium, niobium, copper, nitrogen, etc, To meet the requirements of various applications for the microstructure and properties of stainless steel.
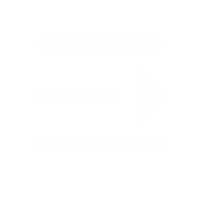
—— Tel:+86-0579-85599004
—— Registered Address: :Rm1101, 11/f San Toi Building No.139 Connaught Rd Central Hongkong
—— Office Address:Room1507, Building 2, City View, No.508 Binwang Street, Yiwu, Zhenjiang, China